Der Scheibenbremsbelag | HELLA
Allgemeines
Ein wichtiges Konstruktionsteil der Bremsanlage ist der Bremsbelag. Zusammen mit der Bremsscheibe bildet der Bremsbelag, auch Reibbelag genannt, eine Verschleißbehaftete Reibpaarung und muss extremen Belastungen standhalten.
Um in jeder Bremssituation die bestmöglichen Ergebnisse zu erzielen muss die Materialzusammensetzung der Bremsbeläge an die jeweilige Bremsanlage angepasst werden.
Aufbau Scheibenbremsbelag
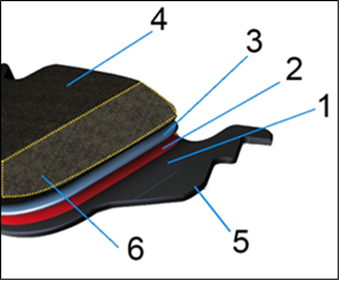
Der Bremsbelag hat einen schichtweisen Aufbau.(Abb.)
1. Trägerplatte
2. Kleber
3. Zwischenschicht
4. Reibmaterial
5. Pulverbeschichtung
6. Sekundärmaßnahme
Als Basis des Bremsbelages dient eine pulverbeschichtete Trägerplatte aus Stahl. Diese wird der jeweiligen Bremsanlage in entsprechender Güte, Festigkeit und Toleranz individuell der Anforderung angepasst.
Sie hat die Aufgabe die Temperatur abzuleiten und den Belag im Bremssattel zu führen. Die Pulverbeschichtung gibt der Trägerplatte einen zuverlässigen Korrosionsschutz. Auf diese Trägerplatte wird der Kleber aufgebracht. Speziell entwickelte Kleber verbinden dauerhaft die Belagmasse mit der Trägerplatte und gewährleisten darüber hinaus eine hohe Abscherfestigkeit. Darauf folgt die Zwischenschicht auch Underlayer genannt. Sie verbessert Härte, Rissverhalten und die Komforteigenschaften des Bremsbelages.
Als letztes wird das eigentliche Reibmaterial aufgebracht. Das Reibmaterial hat anspruchsvolle Aufgaben zu erfüllen und wird deshalb exakt auf den jeweiligen Verwendungsbereich abgestimmt. Jeder Hersteller verwendet hier seine speziellen Rezepturen die verständlicherweise geheim gehalten werden. Zusätzlich können am Bremsbelag Sekundärmaßnahmen angebracht sein.
Diese Maßnahmen und Vorrichtungen bewirken eine zusätzliche Verbesserung von Bremswirkung und Fahrkomfort. Dazu gehören zum Beispiel das abgeschrägte Reibmaterial oder auch auf der Trägerplatte angebrachte Dämpfungsbleche.
Anforderung Bremsbelag
Die funktionalen Anforderungen an einen Bremsbelag im Kraftfahrzeug teilen sich in die Kategorien Sicherheit, Komfort und Wirtschaftlichkeit auf.
1. Sicherheit
- Hohe Standzeit durch mechanische Festigkeit und hohe Temperaturbeständigkeit (bis 800°C).
- Stabilität des Reibwertes unter allen auftretenden Bremsbedingungen
- Unempfindlichkeit gegen Umwelteinflüsse wie Wasser und Schmutz
- Gute Einlaufeigenschaften
2. Komfort
- Keine Geräuschbildung oder Schwingungen
- Geringe Betätigungskräfte am Pedal
- Keine Umweltbelastung durch Abrieb
3. Wirtschaftlichkeit
· Geringer Verschleiß des Reibbelages und der Bremsscheibe
· Geringes Gewicht
· Günstige Produktionskosten
Eine weitere nicht unwesentliche Anforderung ist natürlich auch die Qualität eines Bremsbelages. Aufgrund der Vielzahl der Hersteller wurde seitens der Europäischen Union (EU) folgendes festgelegt.
Innerhalb der EU dürfen nur Bremsbeläge, welche der Regelung ECE-R90 entsprechen, in dem dafür freigegebenen Fahrzeug verbaut werden.
Eine entsprechende Kennzeichnung befindet sich auf der Rückenplatte des Bremsbelages.
Rohstoffzusammensetzung des Reibmaterials
Im Automobilbereich unterscheidet man zwischen Semi-Metallic Belägen (Metall >50%) und Faseraustausch Belägen (Metall < 25%).
Zur Herstellung des Reibmaterials können mehrere hundert verschiedene Rohstoffe verwendet werden.
Diese Rohstoffe kann man in folgende Gruppen einteilen:
Durchschnittlich enthalten aktuelle Rezepturen 25 unterschiedliche Rohstoffe.
Die Verwendung von Asbest im Reibbelag, ist in der EU seit der Einführung der Asbest-Verordnung verboten.