Bremsscheibe | HELLA
Allgemeines
Seit Einführung der Scheibenbremsanlage im Automobil ist die Bremsscheibe ein wichtiges Konstruktionsteil im Automobilbau.
Zusammen mit dem Bremsbelag bildet die Bremsscheibe eine verschleißbehaftete Reibpaarung und muss extremen Belastungen standhalten.
Beide Bauteile sorgen für das notwendige Bremsmoment, um ein Kraftfahrzeug zu verzögern bzw. bis zum Stillstand abzubremsen. Dieses Bremsmoment überträgt die Bremsscheibe auf die Radnabe und von dort auf die Felge.
Aufgrund der thermischen Belastung an der Radbremse hat die Bremsscheibe auch die Aufgabe die entstehende Wärmebelastung abzuführen.
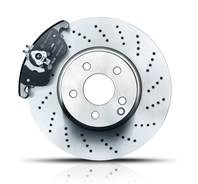
Material
Bremsscheiben sind hohen mechanischen Belastungen beim Bremsen ausgesetzt. Sie müssen neben Druckkräften, Zugkräften und Fliehkräften auch thermischen Belastungen standhalten. Um in jeder Bremssituation die bestmöglichen Ergebnisse zu erzielen, muss die Materialzusammensetzung von Bremsscheibe und Bremsbelag aufeinander abgestimmt sein. Je nach Fahrzeugtyp und Anwendungsbereich, können Bremsscheiben aus den Materialien Grauguss, Edelstahl, Carbon oder Keramik gefertigt sein. Der größte Teil wird aus Grauguss gefertigt, dessen Eigenschaften man durch Zugabe unterschiedlichster Materialien verbessert. Durch Zugabe von Molybdän und Chrom verbessert man das Wärmerissverhalten und die Verschleißfestigkeit der Legierung. Die Wärmeaufnahmefähigkeit wird durch die Erhöhung des Kohlenstoffgehaltes verbessert.
Bremsscheiben aus Keramik oder Carbon werden aus Kostengründen im Motorsport oder bei hochpreisigen Fahrzeugklassen eingebaut. Neben dem geringen Gewicht, der hohen Lebensdauer und dem guten Ansprechverhalten, ist ein weiterer Vorteil das geringe Fadingverhalten.
Aufgrund der schlechteren Wärmeleitfähigkeit benötigen diese Bremsscheiben aber spezielle Bremsbeläge, die diesen Faktor wieder ausgleichen.
Bauarten
Während des Bremsvorganges wird durch die Reibung, Bewegungsenergie in Wärmeenergie umgewandelt. Bis zu 90% dieser umgesetzten Energie wird von der Bremsscheibe aufgenommen und an die Umgebungsluft abgegeben.
Dadurch können unter Extrembedingungen Temperaturen bis zu 700°C an den Radbremsen entstehen. Neben den physikalischen Belastungen sind Bremsscheiben zusätzlich Umwelteinflüssen, Schmutz, Wasser und Salz ausgesetzt. Alle diese Faktoren müssen bei der Konstruktion seitens der Bremsscheibenhersteller berücksichtigt werden und fordern unterschiedliche Ausführungen von Bremsscheiben. Grundlegend unterscheidet man hier zwischen massiven und innenbelüfteten Bremsscheiben (Abb.1).
Eine massive Bremsscheibe ist aus einem Guss und hat nur einen Reibring. Da massive Bremsscheiben Wärme nur langsam abgeben können, werden diese in der Regel im Kleinwagensegment verbaut. Bei schweren oder hochmotorisierten Fahrzeugen finden diese vor allem an der von der Bremsleistung her geringer belasteten Hinterachse Anwendung. Aufgrund der besseren Dosierbarkeit ersetzen sie dort teilweise die Trommelbremse.
Innenbelüftete Scheiben haben aufgrund Ihrer größeren Masse ein besseres Wärmespeichervermögen und kühlen durch die luftdurchströmten radialen Kanäle (Abb.2) schneller ab. Diese radialen Kanäle liegen zwischen den beiden Reibringen. Durch die Drehung der Bremsscheibe entsteht eine Ventilatorwirkung, die einen ständigen Luftzug durch die Bremsscheibe bewirkt.
Da durch die dynamische Achslastverteilung die größeren Bremskräfte an der Vorderachse anfallen, werden belüftete Bremsscheiben in der Regel an der Vorderachse verbaut. Somit wird unter Extrembedingungen eine hohe Bremsleistung gewährleistet. Je nach Fahrzeugtyp, Anwendung oder Motorisierung können innenbelüftete Bremsscheiben auch an Vorder- und Hinterachse verbaut sein.
Zusätzlich können massive und innenbelüftete Bremsscheiben mit Schlitzen oder Nuten versehen oder axial gelocht sein. Bremsabrieb, Wasser und Schmutz wird in den Schlitzen oder Nuten gesammelt und durch die Drehbewegung nach Außen abgeführt. Die axialen Bohrungen erhöhen die Wärmeabfuhr, haben aber keinen Selbstreinigungseffekt da sich Bremsabrieb in den Löchern ablagern kann.
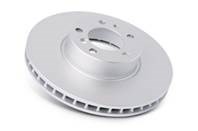
Abb.1
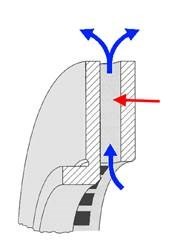
Abb.2
Varianten
Je nach Fahrzeug-, oder Bremssystemkonstruktion können Bremsscheiben, die an der Hinterachse eines Fahrzeuges verbaut sind, gleichzeitig im Scheibentopf eine Bremstrommel für die Handbremsvorrichtung integriert haben.
Ebenfalls werden von einigen Herstellern auch Radlager und Impulsringe des Antiblockiersystems (Abb.3), bereits in die Bremsscheiben integriert. Beide Ausführungen verlangen vom Techniker im Rahmen der Reparatur ein erhöhtes Maß an Sorgfältigkeit. Um den Korrosionsschutz zu verbessern, werden Bremsscheiben teilweise beschichtet. Diese Bremsscheibe kann komplett oder außerhalb des Reibringes mit einer Anti-Rost Lackierung überzogen sein. Gleichzeitig wird dadurch der optische Eindruck im offenen Felgenbereich der Radbremse verbessert. Ist die Bremsscheibe vollständig beschichtet, wird ein moderates Einfahren empfohlen, bis sich Bremsbelag und Scheibe aufeinander angepasst und sich die Lackschicht auf dem Reibring durch die Reibung abgelöst hat.
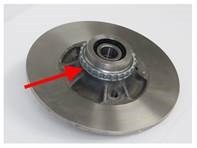
Abb.3
Fehlerdarstellung Bremsenrubbeln
Hierbei handelt es sich um niederfrequente Schwingungen am Fahrzeug die durch das Bremsen ausgelöst werden.
Hier unterscheidet man zwischen Kaltrubbeln und Heißrubbeln.
Kaltrubbeln macht sich durch ein Flattern des Lenkrades, Bremskraftschwankungen oder durch ein pulsierendes Bremspedal bemerkbar. Ursache hierfür ist ein Dickenunterschied der Bremsscheibe der auf ungleichmäßigen Verschleiß zurückzuführen ist und sich bei gelöster Bremse darstellt. Die durch den Seitenschlag verursachten Auswaschungen des Reibringes führen während der Drehung zu einem periodischen Kontakt der Bremsscheibe an den Bremsbelag. Heißrubbeln entsteht durch reversible Bremsscheibendeformation, die mit einer ungleichmäßigen Erwärmung der Bremsscheibe gekoppelt ist. Durch Überhitzung kann sich der Reibring der Bremsscheibe nach außen oder innen unzulässig verformen. Verstärkt wird diese noch durch lokale Hitzezonen (Abb.4) auf der Bremsscheibe. Ursache dafür kann ein Untermaß der Bremsscheibe, verschlissene Bremsbeläge der auch die Verwendung von Bremsenprodukten sein, die nicht der Herstellerspezifikation entsprechen.
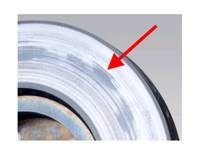
Abb.4
Verschleiß und Prüfung
Aufgrund der hohen mechanischen und thermischen Belastungen und durch die zusätzliche Umweltbelastung sind Bremsscheiben einem natürlichen Verschleiß ausgesetzt. Der Zustand der Bremsanlage sollte deshalb regelmäßig und im Rahmen der vom Hersteller vorgegebenen Inspektion geprüft werden. Die Verschleißgrenze der Bremsscheibe wird seitens des Herstellers in Form einer Mindestdicke des Reibringes festgelegt. Dieser Wert in Millimeter wird auf dem Außenrand (Abb.5) der Bremsscheibe angegeben bzw. eingestanzt. Dieser Wert ist so bemessen, das nach Erreichen dieser Dicke, bei normaler Fahrweise und unter Betrachtung der vorausgegangenen Wechselintervalle der Bremsbeläge, noch ein Satz Bremsbeläge verbaut werden könnte. Sollte hier seitens der Werkstatt keine Information vorliegen, ist es ratsam Bremsscheiben und Beläge zu ersetzen.
Zusätzliche Prüfungen sind der Rundlauf (Scheibenschlag) und die Dickendifferenz (unterschiedliche Scheibenstärke) der Bremsscheibe.
Die Prüfung des Rundlaufs von Bremsscheiben erfolgt im eingebauten Zustand (Abb.6). Dabei wird mit einer Messuhr, die ca. 10 - 15 mm unterhalb des äußeren Scheibenradius angesetzt wird, die Messung durchgeführt. Die Abweichungen sollten, gemessen über mehrere Radumdrehungen, bei neuen Fahrzeugen 0,070 mm und bei älteren Fahrzeugen aufgrund der größeren Toleranzen 0,10 mm nicht überschreiten. Diese Prüfung ist nur bei neuen Bremsscheiben aussagefähig. Bei Abweichungen sollte der Zustand von Radnabe und Lager als zusätzliche Fehlerquelle in Betracht gezogen werden.
Die Messung der Dickendifferenz des Reibrings einer Bremsscheibe kann exakt nur mit Spezialgeräten gemessen werden. Mit hinreichender Genauigkeit kann dieses jedoch mit einer Mikrometerschraube erfolgen, die eine Messgenauigkeit von ± 0,001 mm aufweist. Hierbei sollten an 12 bis 15 Stellen des Umfangs sowie ca. 10 – 15 mm unterhalb des äußeren Reibradius gemessen werden. Je nach Fahrzeugtyp können Dickendifferenzen von 0,012 mm bis 0,015 mm bereits zu Rubbelerscheinungen führen. Deshalb dürfen diese Werte bei neuen Scheiben nicht überschritten werden.
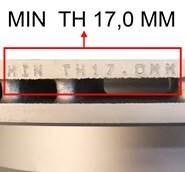
Abb.5
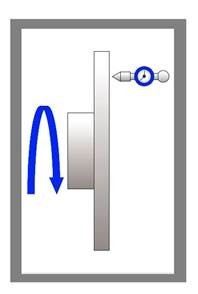
Abb.6
Wartungshinweis
Um eine einwandfreie Funktion zu gewährleisten werden folgende Hinweise empfohlen:
- Bremsscheiben sollten immer paarweise getauscht werden
- Neue Bremsscheiben immer mit neuen Bremsbelägen verbauen
- Die Auflagefläche der Radnabe sollte plan, gratfrei, sauber, rostfrei und ohne Beschädigung sein.
- Bei innenbelüfteten Bremsscheiben ggf. die Laufrichtung beachten
- Korrosionsschutz vollständig mit geeignetem Reinigungsmittel entfernen.
- Vorgeschriebenes Anzugsdrehmoment beachten
- Da sich Bremsscheiben und Bremsbeläge erst anpassen müssen, Bremsanlage moderat einfahren. Herstellerangaben beachten
- Unnötige Gewaltbremsungen in den ersten 100 KM vermeiden
- Produktspezifische Beipackzettel beachten
- Montageanweisungen des Fahrzeugherstellers beachten
- Die Reparatur an der Bremsanlage sollte nur von geschultem Personal durchgeführt werden